top of page
K-Lamp
Kinekt Design
MY CONTRIBUTION: ADJUSTABLE LOCKING HINGE
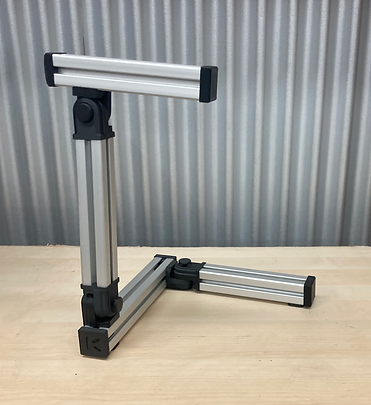

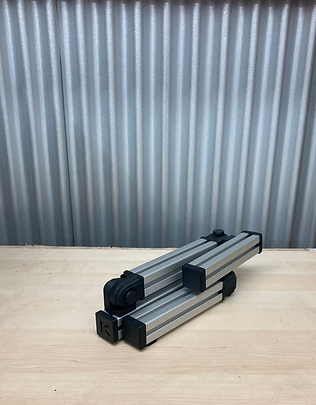
My job for this project was to bring the product concept to life!
In practice, this means I spend my days prototyping, testing, and iterating. Here is a brief glimpse at what that looks like at the Kinekt Design FabLab.

Early idea exploration
This idea to have an ovular button that stays parallel to the beam as it rotates didn't get the votes but was a personal favorite of mine.

Hardware was intentionally concealed within the product to maintain a clean, seamless appearance.

The conical teeth of bevel gears were chosen for the lock because of their ability to better slide into position when meshing & increased surface area.
Ideation on various ways a spring loaded locking mechanism could work.
Conceptualization
Renderings were made to illustrate to the team how the assembly could hypothetically come together.
We then discussed as a group which parts were cool and should stay and which could be reimagined.
For example- I was confident that having a bolt imbedded within the button was necessary but after our pow-wow session it became apparent to me that it was completely unessential.
Each iteration either solved a problem
or taught me a way not to solve the problem.
Problem 1: Piston Snapping


The first piston prototype snapped after little more than the torque of the beam, so a more robust version needed to be designed.
top
bottom
side
Full assembly diagram
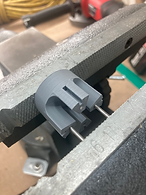

Thicker, denser, skirts, reinforced with metal dowels were inserted to strengthen the piston's weak point.
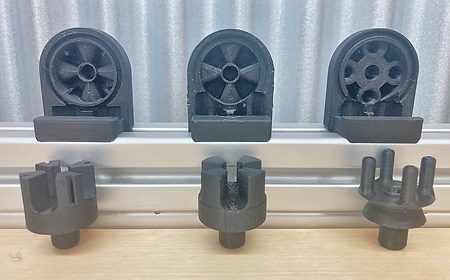
2
1
3
Testing, testing
The piston went from snapping from the weight of the 8020 beam to being able to hold 8kgs at an 8" lever arm with ease.



A stress test to the point of failure was done where at 10kg the gears slipped but the piston itself remained in tact.
Problem 2: Strenuous Assembly
The interlocking ridges of the hinge allows it to house the spring (which rests at a state of compression) without self destructing.
This form however was by nature difficult to assemble.
This problem was solved by rethinking the way the hinge comes together and by making one of the ridge caps screw on via bolt and embedded threaded insert.



AFFORDANCES collapsibility, versatility
Especially useful for packaging, the K-Lamp now collapses to have a 3in² footprint.

With the ability to lock every 15º, each beam can be maneuvered to best navigate your space.


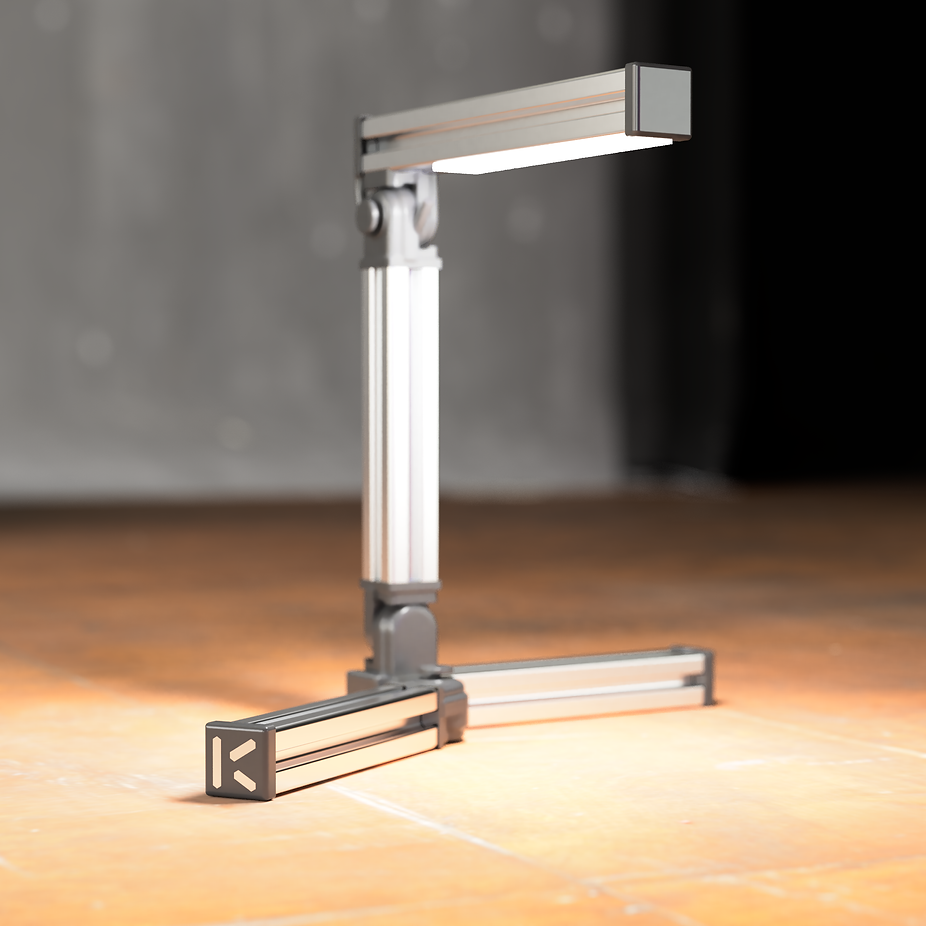
bottom of page